


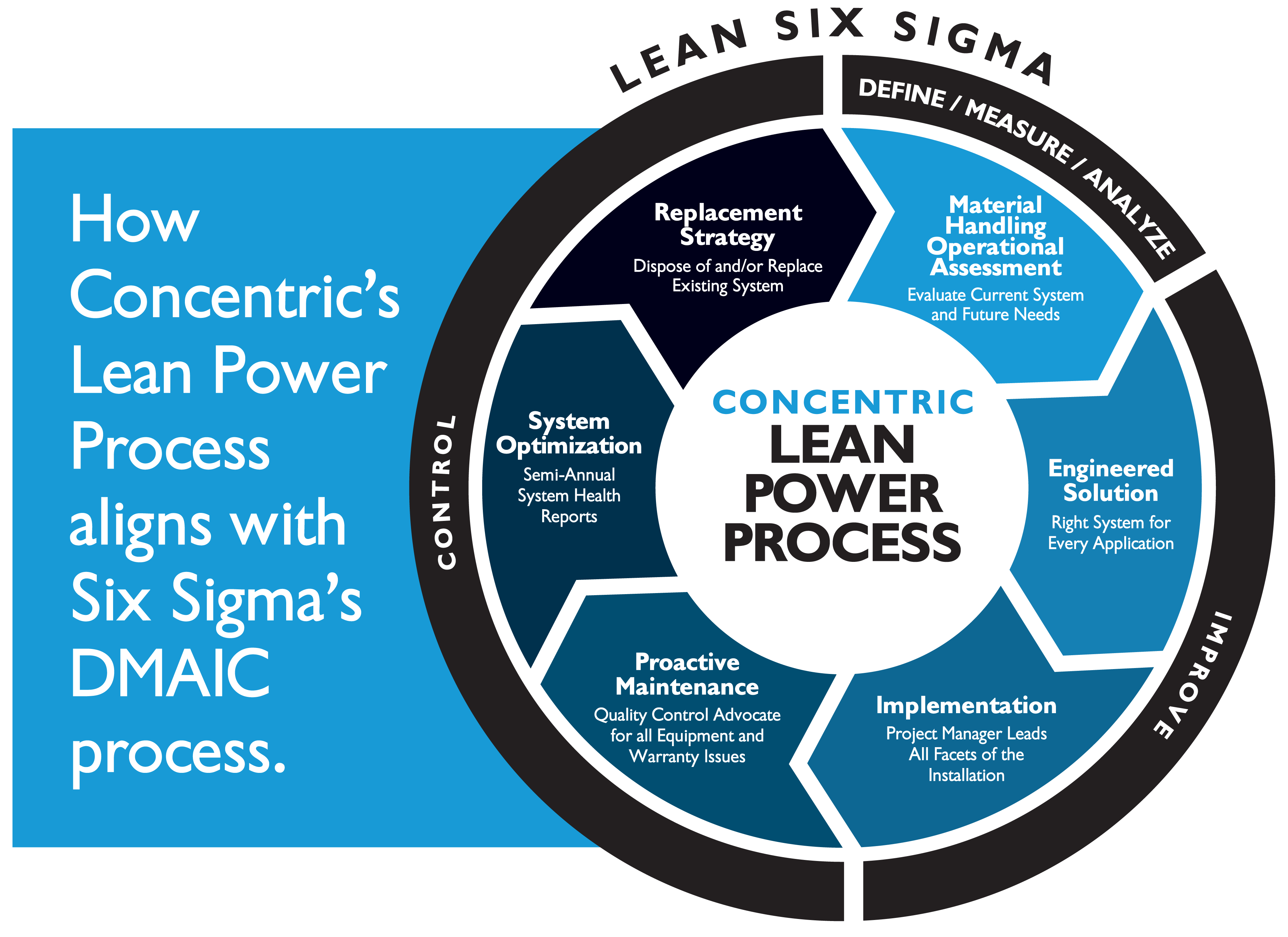
These openings often come in the form of long, intricate processes that leave significant room for mistakes and resource waste. Once the problem is identified, it’s time to look for ways to nullify defects. Gathering data that shows where a specific problem lies helps to concentrate on correcting that area.

Establishing a clear standard of quality in the early stages defines what the customer/market demands.ĭuring the implementation process, it’s easy to get caught up in the whirlwind of changes and lose focus on the initial problem. The primary goal of any change in the implementation process should be to deliver maximum benefit to the customers. Also, owing to the versatility of Six Sigma and its applications, Six Sigma certification is highly regarded and sought-after across many industries and domains. The defect rate is said to be extremely low (3.4 times per million) when the process exhibits Six Sigma. The name Six Sigma is derived from the bell curve used in statistics where one Sigma represents one standard deviation away from the mean. Today, companies the world over use Six Sigma to improve the processes, which help bring about positive changes in the organization. It is because of the success that GE enjoyed that people began implementing Six Sigma programs into their organizations. General Electric (GE) was the first to use Six Sigma in its operations in order to reduce waste, improve the quality of the product and in turn save money. This original idea still forms the core of Six Sigma methodologies with a few more additions, which include improving process with regards to interaction and product design. It was in the early 1980’s that Bill Smith at Motorola developed Six Sigma principles in order to measure defects and improve overall quality. Sign Up For Lean Six Sigma Training And Certification Origin of Six Sigma Today, Six Sigma is used as one of the major themes for Total Quality Management (TQM). All in all, Six Sigma is customer centric and its main objective is to deliver value, reliability as well as high performance to the customer. This method uses statistical data and creates a special infrastructure of people, also called experts within the organization.Įvery Six Sigma project is carried out as part of an organization following a defined sequence and has quantified financial targets. Basically, Six Sigma uses a set of quality management methods of doing the above. The main objective of Six Sigma is to implement a process, which systematically gets rid of inefficiency and defects. If you are on this page I assume you have heard about Six Sigma which is basically a methodology used to improve business functionality. Six Sigma is a methodology used to improve business processes by utilizing statistical analysis rather than guesswork. Lean Six Sigma Online Certification & Training.Six Sigma Virtual Instructor-led Training.
